Pham Xuan Hong, Chairman of the HCM City Association of Garment, Textile, Embroidery and Knitting (AGTEK), said at the event on April 14 that textile-garment is not only a spearhead export industry of Vietnam but also one of the sectors generating the biggest numbers of jobs, about 2.5 million.
    |
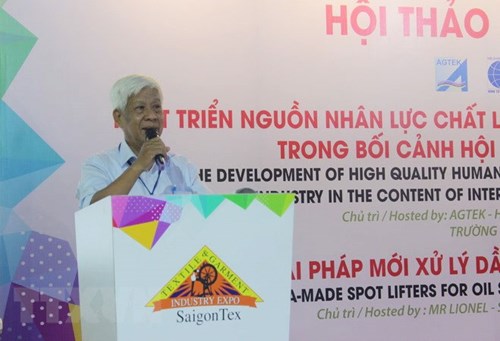 |
AGTEK Chairman Pham Xuan Hong speaking at the worrkshop |
However, most of employees in the sector are manual workers in charge of simple steps while the steps requiring technical skills like dyeing or designing are facing a shortage of skilled workers.
Hong said the shortage of high-quality manpower is also one of the reasons why local production of apparel materials remains undeveloped and Vietnam has to depend on imported materials. Meanwhile, the steps generating high added value like designing products and building brands are still limited.
Although Vietnam is one of the five biggest apparel exporters in the world, global consumers haven’t known any Vietnamese fashion brands, he said.
Dr Pham Xuan Thu from the HCM City College of Foreign Economic Relations said only about 30 percent of over 6,000 textile-garment businesses in Vietnam operate in textiles, including weaving, dyeing, printing and finishing fabric. Most the remaining firms make products ordered by foreign fashion brands. Only few of them are able to create their own products, from manufacturing fabric, designing to making apparel.
Many companies still have to hire foreign experts and technicians at high costs to be responsible for dyeing, completing fabric and designing products, thus augmenting production costs and reducing their products’ competitiveness compared to foreign rivals, he added.
Amidst growing integration and competition, to retain development and engage in global textile-garment value chains, the country needs to invest in training and improving manpower quality in an appropriate manner, participants in the workshop said.
Dr Thu said the textile-garment sector has expanded to a certain size and now it’s time for it to make changes in quality, which means switching to the stage creating more added value.
To do that, the sector has to restructure both production and manpower, he noted, adding that only when labour quality increases can businesses make use of material sources well, raise labour productivity and improve management capacity to boost their competitiveness.
He suggested them invest more in manpower training, recruit and give intensive training to committed employees, and offer appropriate salary and bonus to encourage workers to make self-improvement.
Another problem facing textile-garment companies is that their employees tend to switch to other firms to look for better opportunities after getting training and experience. Therefore, to keep employees, aside from appropriate salary, businesses should also create conditions for workers to show their capacity, create a friendly work environment and pay attention to workers’ spiritual needs, Thu said.
At the workshop, AGTEK Chairman Hong also called for more active participation of State management agencies and training schools to boost training in the textile-garment industry.
Source: VNA