    |
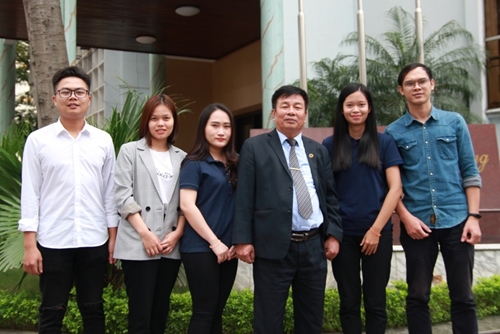 |
Prof. Pham Huy Khang and the students |
However, knowing what the problem is and solving it are two different things. Luckily, a group of students have found their own way to cut waste and protect the environment.
The five students from the University of Transport and Communications in Hanoi have created a mixture of materials with plastic bags as a component to produce bricks that can be used to pave streets.
The idea first sounded strange as materials like asphalt, concrete, stone and sands are more commonly used in the road building industry.
However, the traditional way may have to change as the students have proved plastic can be used to make bricks.
In their research, instead of using concrete as the major material, they used plastic bags.
Their project recently won an outstanding and first prize at the university’s yearly contest for students in scientific research.
It is now competing at a national contest on environmental protection and has been tipped for success.
As part of their research, the team had to experiment on more than 50 samples to find the right ratio between stone, sand and plastic at an adaptable temperature.
“One brick needs 0.9kg of plastic bags to make, so 100 bricks will need about 90kg of plastic bags. If concrete is replaced by nylon bags, large amounts of plastic waste which are released into the environment every day would be consumed,” said one of the group.
Tran The Anh, the group's leader from the Bridge, Road and Airport Faculty, said there was no optimal solution to completely solve the issue of pollution due to huge amount of plastic bags being discharged into the environment.
“So, instead of burying them or waiting for years for them to decompose, we should recycle them into new products. We came up with a plan to recycle them by reproducing them into a useful and safe material,” Anh said.
“Plastic bags are originally made from polymer granules. Based on the knowledge we learned at the university’s Building Materials and Polymer Concrete Faculty, we thought, 'Why not replace the binder of concrete with the polymer from the plastic bags?'"
The group embarked on research in November last year and started experiments this February.
It took two days for them to collect dozens of kilos of plastic waste from a landfill in Hanoi’s Soc Son district.
“The landfill is the gathering place for many different types of waste so we had to dig it all up to find the plastic bags. It took us two days to collect more than 20kg of them,” said Pham Van Duc, another member of the group.
By using what they have learnt, the group then tried making construction materials from sand, gravel and plastic bags.
The bags were washed, cleaned and dried then heated up to a certain temperature.
“It sounds simple but to complete a product, we had to try many times to find a ‘golden ratio’ between the aggregates: 50-60 per cent of stone, 20-25 per cent of yellow sand, 5-10 per cent of stone powder and 25 per cent of plastic bags,” Anh explained.
As it was run by students, the project had financial support of a mere 600,000 VND (26 USD).
Experts have said bricks made with plastic material at an appropriate ratio could be used for paving roads as they are highly durable, can be easily used for paving and can partly help solve the issue of plastic waste.
A brick is about 3.7kg weight and it needs 0.9kg of plastic bags to produce.
Viphavady Inthapatha, a student from Laos, who is also a member of the group, has strong memories about the time he joined the group to collect plastic bags in the landfill.
“We travelled by motorbikes to Soc Son landfill which looks like a mountain of rubbish. Wearing gloves and masks, we started to pick up each plastic bag from the pile,” said Inthapatha.
According to Duc, during the experiments, their biggest challenge was finding the appropriate mixing ratio between the materials.
The group first wasted a lot of time cutting plastic bags into small pieces for testing because they thought the whole bags, when heated, would burn and mix unevenly.
However, when they cut them into small sizes, the plastic immediately shrunk and clumped without cohesion.
They had to redo it again and again until they found that keeping the original size of the bags and reheating them would create an adhesive material that helps increase the product's durability.
“We had to test more than 50 different samples over and over to find the standard mixing ratio between stone, sand and plastic. Stone acts as a material with high strength, sand helps fill the voids between stones and plastic acts as a binder,” Duc said.
The materials were mixed and heated together at about 180-220 degrees Celsius.
During the heating process, the mixture is constantly and evenly stirred so that melted plastic can flow and stick together to the aggregate particles.
The mixture will be immediately poured into a mould and compacted by machines, hammer or compactor to make the final products.
Although they faced many difficulties during the process, the students stuck to their task and spent most of their spare time on experiments.
The students received support from their teacher, Prof Pham Huy Khang who provided them with space and equipment for their experiments at the university, including mixing and pressing machines and a compactor.
“Their product is very feasible, applicable and practical to reality as it will help solve part of the problem of plastic waste pollution in our country. This product, if further improved, can be put into application for paving streets," Khang said.
"Production costs will certainly not be more expensive than existing products in the market. But if you take into account the environmental value, the efficiency should not be counted by money.”
Source: VNA